Terminal automation system: what is and how it works
A terminal automation system is essential to the oil and gas industries. It can automate different manual processes in a terminal, specifically around truck loading and unloading, additive injection, blending and control of rail/pipeline/marine operations/tank transfers, providing tailored documentation and reporting. A good terminal automation system must be flexible and work with meter skids, weight scales, and tank gauging systems.
On this page we will focus on:
- What is a terminal automation system
- Its main features
- Benefits and advantages
- Terminal automation system architecture
- ISOIL solution SBR Badge Reader
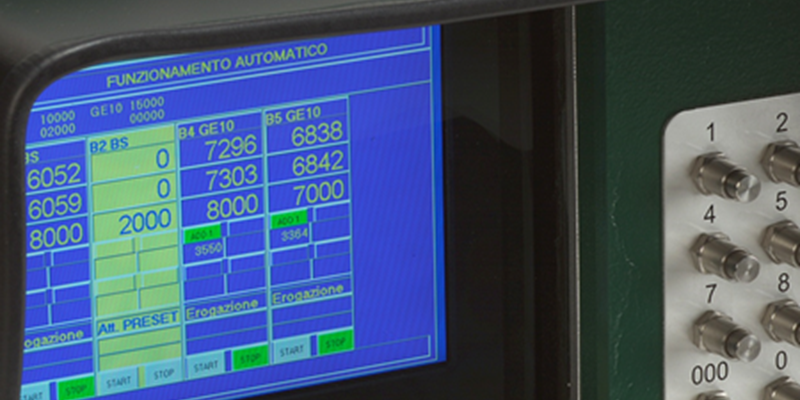
What is a terminal automation system?
An automated terminal system allows remote control of loading/unloading points in oil terminals, monitoring and controlling the loading process of tank trucks to ensure reliable and safe operations. The TAS is critical in the oil industry, both in big and small systems.
Do you need more info about our terminal automation systems?
Contact us
The main features of a terminal automation system
As terminal operation numbers continue to increase, industries are seeking ways of improving productivity and efficiency to meet Customers' needs. Today’s terminals handle increased volumes and greater capacity. That’s why terminal operators need automated processes in order to stay competitive and profitable.
A terminal automation device must have some main characteristics to be reliable and ensure control in key sectors such as oil & gas. Some primary features are:
- Loading authorizations and safety
- Driver’s PIN/card validation
- Validation of preset quantities
- Multi-compartment loading
- Additive check
- Combination of control interfaces with third-party systems
- Real-time display of dynamic information
- Graphic display of the individual tank’s status
- Real-time events recording of devices status
- Fully connectable via the local network (LAN) of the existing site
All solutions are customizable based on the real needs of the Customer and according to the systems present in the terminal.
Key benefits of terminal automation systems
Process automation offers several benefits for oil installations.
Process optimization
The work of the entire staff is completely optimized. Thanks to the sophisticated computerized control systems it is possible to monitor the entire liquid distribution chain within the loading facilities.
Elimination of errors
Thanks to our systems, the possibility of accidental or even voluntary errors is nullified with regard to the preparation of administrative and fiscal documents both for loading and for travel for each load carried.
Full monitoring
Each truck is constantly monitored during the entire loading process. The monitoring also includes automatic control and implementation of all safety procedures, before carrying out loading for the subsequent stages of delivery.
Verification of distribution
Other features: no risk of overload and attempts at fraud, constant control of the product with respect to the types and quantities supplied, automatic preparation of the necessary transport documents, thus reducing the overall loading time for each vehicle.
The architecture of terminal automation systems
The terminal management system architecture consists of different devices. These include workstations, engineering stations, servers, printers, and communication with field elements such as flow computers, card readers, weight bridges, and tank gauging systems.
SBR Badge Reader for terminal automation
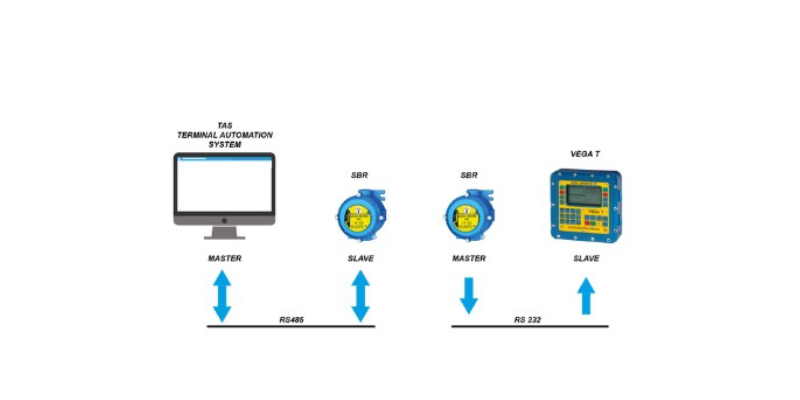
Automation of tank truck loading procedures includes user recognition as a safety and fraud prevention requirement. Among the numerous available methods with various degrees of security (from simple PIN to biometric devices), badge reading is a very widespread method. The SBR contactless badge reader for installation in classified areas reads the badge in radiofrequency and holds it inside the specific housing throughout the entire loading operation. Its removal entails the immediate interruption of procedures.
Designed as an important component of the terminal automation procedure, it can work directly combined with the electronic counter (VEGA T and VEGA 3) in MASTER mode or as a remote device in communication with the control room in SLAVE mode.
Do you need more info about our Terminal Automation Systems?
Contact us
Contact us for more information about our services and products
Form sent successfully
Error