Side-stream Blending
Alcohol Blending in the Oil Industry
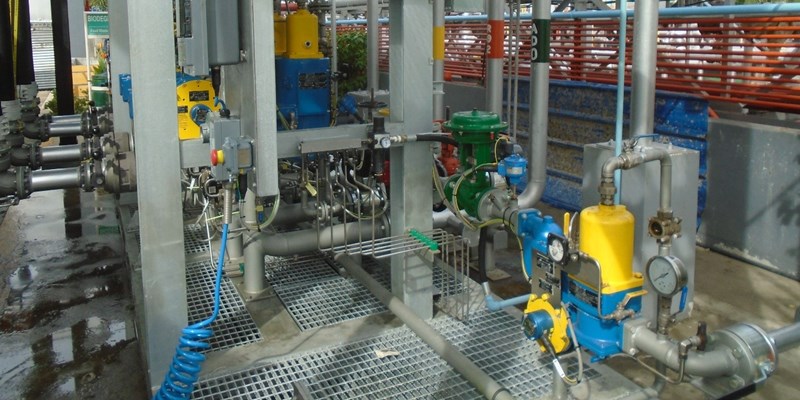
When trying to minimize environmental impact and reduce costs, fuel blending solutions may be taken into account as an alternative to the consumption of nonrenewable resources.
In this article we'll deepen the following:
- The Importance of Fuel Blending;
- Sequential Blending, Side stream Blending, Ratio Blending;
- ISOIL Products for Blending Operations.
The Importance of Fuel Blending
The reserves of a nonrenewable resource such as oil are in fact considered economically depleted when 80% of the supply has been used; the remaining 20% is considered too expensive to extract. At the current rate of consumption, global oil reserves will last about 40/45 years. That is why the production of biofuels like ethanol helps conserving fossil fuels and it is an environmentally friendly alternative.
In particular alcohol blending in fuels is a process in which a certain percentage of alcohol, such as ethanol, is added to gasoline. Ethanol-gasoline mixtures burn cleaner and have higher octane levels than pure gasoline also leading to better engine performance and fuel efficiency.
Sequential Blending, Side stream Blending,
Ratio Blending
The process of alcohol blending in fuels is typically done at fuel depots or in refineries. Based on the number of lines and on the point where the alcohol is injected, we can identify different solutions to obtain the required blended product.
Sequential blending refers to the process of blending different fuel components together in a specific order, or sequence through the same metering line.
For example, gasoline might be blended with a certain percentage of ethanol, and then a certain percentage of methanol, in that specific order.
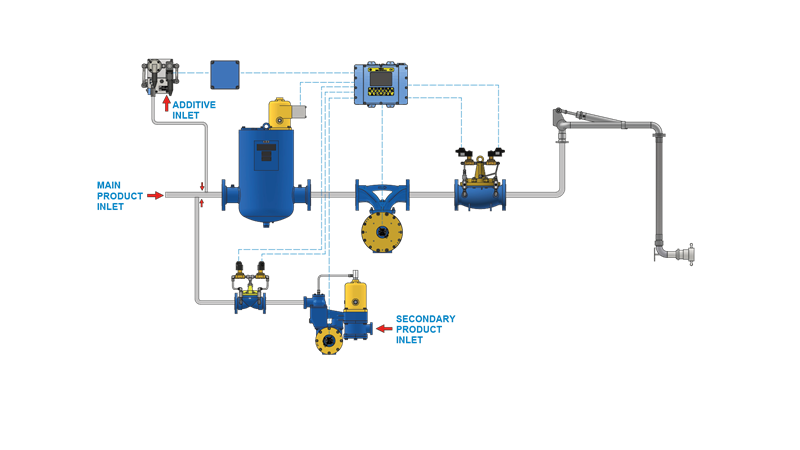
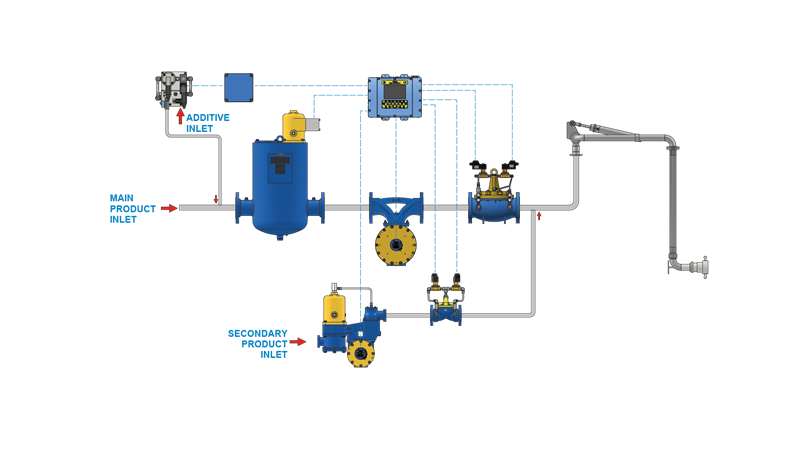
Ratio blending
Side stream blending refers to the process of blending simultaneously two or more products, with injection points upstream the main line.
This type of blending could be used to achieve a specific octane level or emissions profile, directly at the loading point.
For example, a fuel might be blended with a ratio of 90% gasoline and 10% ethanol during the tank track loading.
Ratio blending, refers to the process of blending simultaneously two or more products, with injection points downstream the main line.
This solution will guarantee no problem in case of an emergency stop, providing precise temperature compensation, and the most accurate and self compensating system.
Would you like to learn more about the biodiesel blending process and technologies?
Read here
ISOIL Products for Blending Operations
Since in all such procedures high accuracy and repeatability are required, the instruments used, i.e. meters, electronic flow computers, and valves must be reliable and precise.
In fuel blending operations, p.d meters are used to measure the flow rate of each component of the blend, and to ensure the correct proportion of each component.
ISOIL positive displacement meters, ranging from 1 ½” to 10”, with accuracy of 0.1% and a repeatability of 0.02%, are therefore commonly used for these application.
On the other hand, electronic flow computers also play an important role by providing information about flow rate and total volume of each component of the blend and by performing density, temperature, and pressure calculations.
This information is used to ensure that the final blended fuel meets the desired specifications.
ISOIL VEGA 3 flow computer, certified under the Measuring Instruments Directive 2014/32/UE, can manage up to 12 meters and 6 loading arms simultaneously.
Providing real-time data, VEGA 3 flow computers can also be interfaced with a Terminal automation software (TAS).
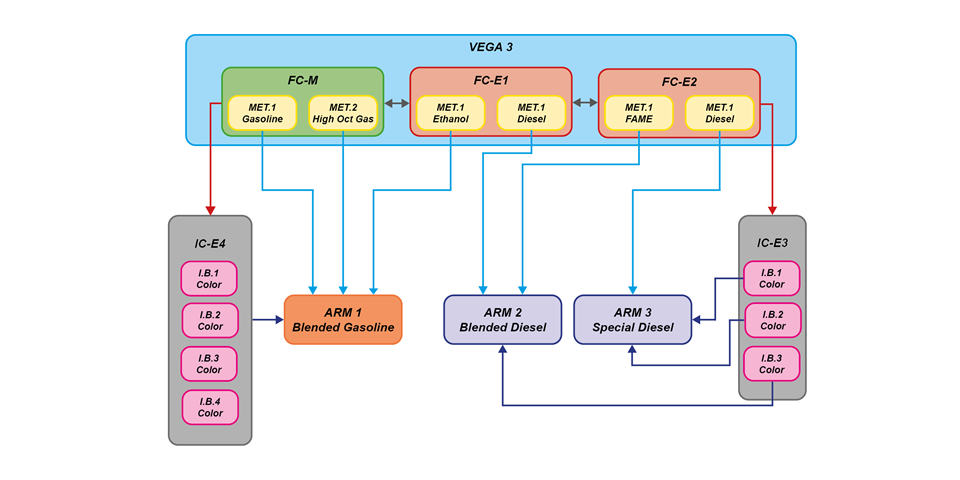
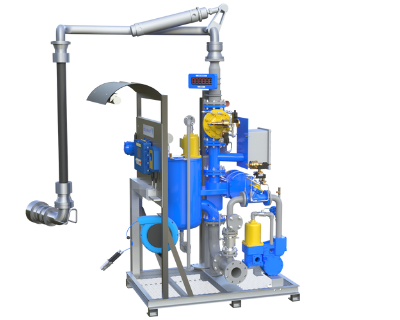
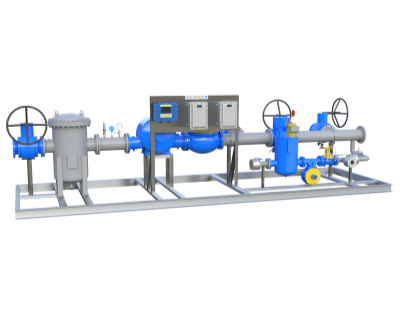
Thanks to its expertise, ISOIL supplies not only pd meters, control valves and electronic flow computers but it can also provide various types of in-line blending skids, designed to meet the specific needs of the customer.
These skids can be installed on the transfer line to the tank or directly at the loading point with the advantage of cost saving solution, faster production time scales, flexibility in blending ratios, and quality of the final blend.
Contact us for more information about our services and products
Form sent successfully
Error