Degassing units
Degassing units for oil terminals are used to remove unwanted gasses from fuels in order to avoid error in measurement. Find out more on how they work and discover ISOIL solutions.
The degassing process is a central step for any metering line in oil terminals.
In fact, in order to ensure accuracy in measurement, it is important to remove any air bubbles before the fluid enters the meter, thus preventing air from being measured.
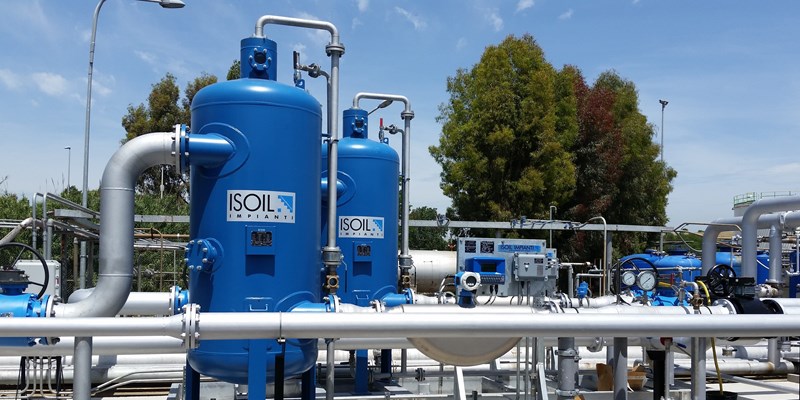
What is a degassing unit?
Degasification units are used to remove unwanted gasses from the liquid: ISOIL gas separators are specifically designed to ensure high efficiency by complying with OIML R117 recommendation.
Working principle
When entering the air separator, the fluid flows through a basket which is made of a filtering cartridge. In this way, foreign particles in the fluid are held by the strainer and dropped on the bottom so that they can be removed through the lower drain plug. Furthermore, since the design and assembling of measuring instruments must guarantee a high-level metrological standard, the degassing unit has been designed to convey eventual air outside the gas separator through the use of a floating ball valve connected to a specific vent valve.
Discover how degassing units are used in helicopter refueling systems.
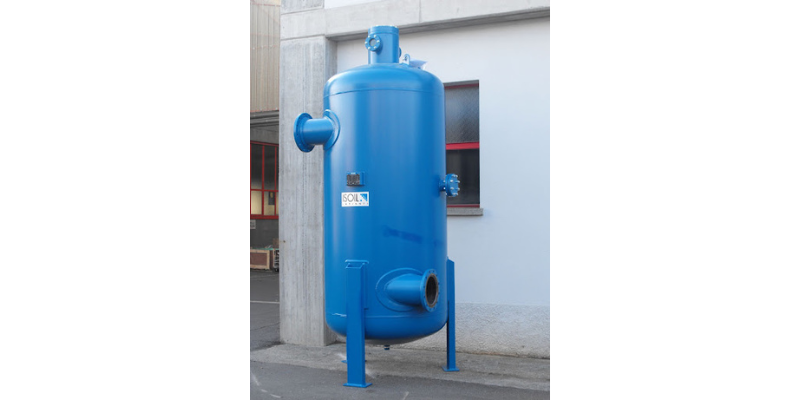
In normal conditions, the level of liquid inside the strainer air separator makes the sphere of the air vent valve float. If air flows through the strainer air separator, gas moves to the upper part thus making the level of fluid decrease. The sphere is no longer supported by the fluid and when it goes down the air vent valve opens. In this way, the gas is discharged.
When the level of liquid starts rising again, the upward movement of the floating sphere closes the valve.
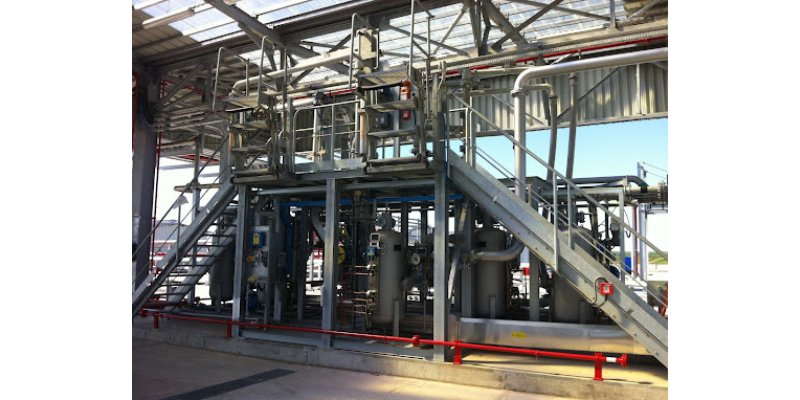
Degassing units for oil terminals
ISOIL series of degassing units are essential, as they prevent the meter from measuring air or gas in the liquid, a fact which would affect measurement accuracy. Moreover the union of both strainer and air separator in a single device allows a reduction in space for installation.
- The FDA and SFDA series of strainer air separators performs the important task of protection against solid particles carried by the fluid and remove air or gas from the liquid. Putting together filtering and air elimination results in a more compact device, thus reducing the size of the group.
- The choice of the filtering net must consider the characteristics of the liquid to be measured. We recommend 100 mesh for gasoline, 60 mesh for diesel, and 40 mesh for fuel oils.
- The DSH and DSV series of strainer air separators are specifically designed to guarantee a high-level metrological standard. Therefore, the strainer conveys eventual air into the gas-separator: the more air in the system, the more the floating-sphere sinks, thus opening the air vent valve.
- The opening of the air-separator activates a micro-switch. This in turn closes the automatic valve stopping product delivery. When all the air has been vented out, the rising level of fluid makes the sphere rise up again and the mechanism closes the air-strainer. Such movement activates the micro-switch again which opens the automatic valve allowing for product delivery.
- ISOIL DV centrifugal air separators perform the same function of the FDA series, i.e. filtering and air elimination, but they exploit rotary motion to do so. Inlet and outlet are in fact placed tangentially to the centrifugal gas separator, so that the fluid is set into motion. This motion together with the long lasting residence time of the liquid inside the equipment allows for efficient separation of air/gas from the fluid while foreign particles are dropped on the bottom where they can be drained by using a bottom plug.
Different solutions are available, depending on flange diameter and plant requirements.
Find out more